Delivering safe and reliable drinking water for remote communities
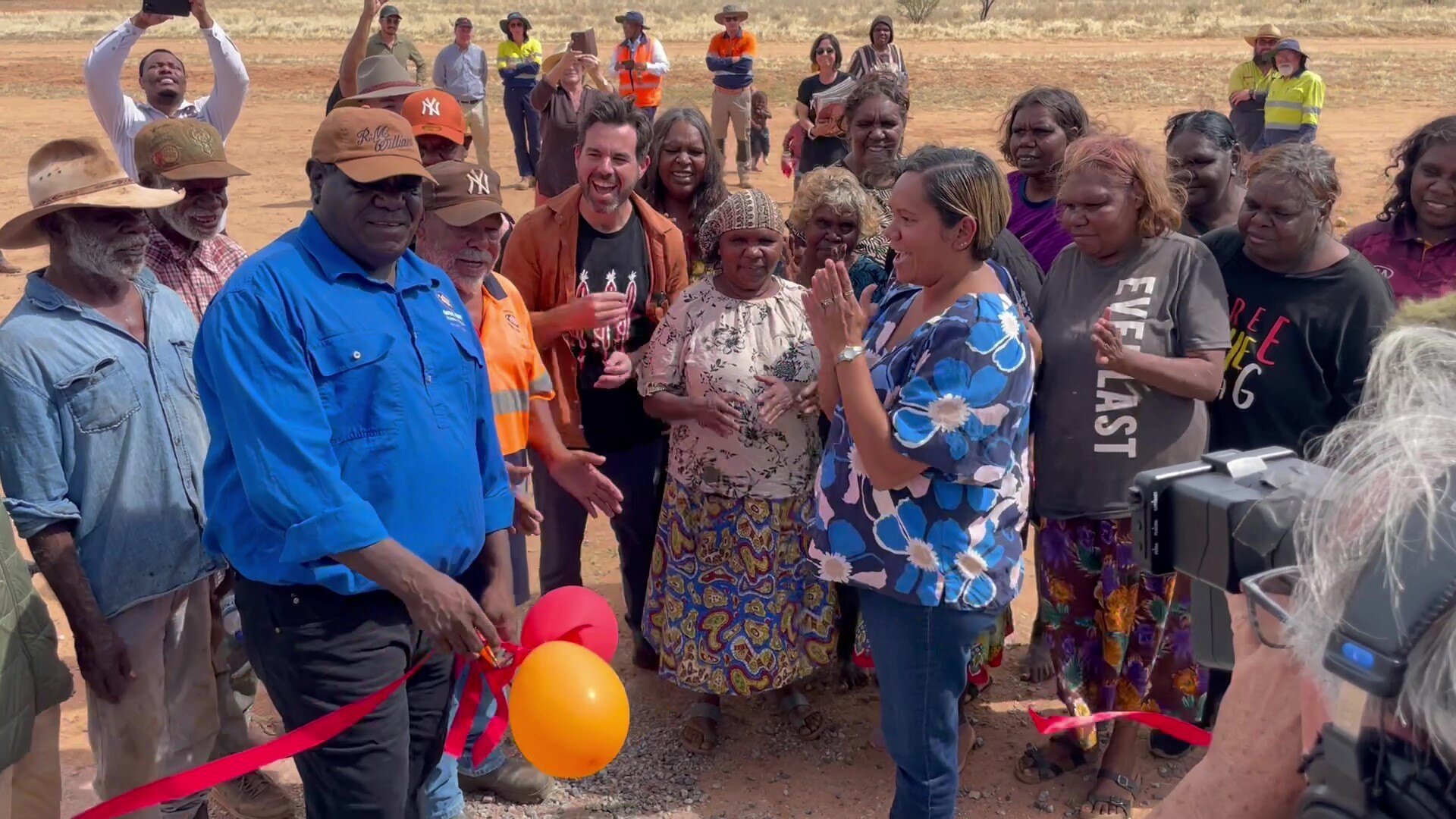
Providing safe and reliable drinking water is particularly challenging within remote locations, but one award winning project has shown how far commitment and collaboration can go in providing fit-for-purpose technology for regional communities.
Sponsored by SMEC, the Infrastructure Project Innovation Award (Regional) was presented to Power and Water Corporation and Clean TeQ Water at Ozwater’24 for the outstanding work in delivering the Laramba Treatment Plant in the Northern Territory.
The Australian Water Awards stand to recognise innovation and excellence within the water community, with state and territory project awards now open for nominations.
Located about 200kms northwest of Alice Springs, the Laramba community was reliant on groundwater containing naturally occurring levels of uranium that exceed the Australian Drinking Water Guidelines recommended level.
In response to the consistently elevated uranium in the water supply, as well as strong advocacy by community members, Power and Water Corporation engaged Clean TeQ Water to deliver a customised 360 m3/d ion exchange plant for the community.
SMEC National Manager Dan Spackman said the project is a wonderful example of how the water sector can implement real innovation to improve the lives of communities.
“SMEC is proud to continue its sponsorship of the Regional Infrastructure Project Innovation Award for the Australian Water Association, and it is so pleasing to see a project like the Laramba Water Treatment Plant receive the award this year,” he said.
“The project resulted in a reduction of uranium levels in the drinking water supply to almost undetectable levels and provided water security to some of the most vulnerable Indigenous communities in the Territory – that's certainly something worth celebrating.”
Remote challenges
Power and Water Corporation’s Dr Nazrul Islam said the project was particularly challenging due to the remote location combined with a six-month timeframe from contract signing to plant handover.
“The Laramba community was advocating for some time for better quality drinking water. The community was working with local representatives and councils, they wanted to ensure the water was safe for them and their children,” he said.
“We were given a very tight timeframe to deliver the project. The site was not accessible by land throughout the year. There were periods when we could not reach the site due to seasonal flooding.
“Given the six-month delivery deadline, we had to plan everything sequentially, while also working across multiple teams and stakeholders.”
Power and Water Corporation Chemical Engineer Megan Purser said the remote operating site posed significant challenges, not only with delivery but also with ongoing maintenance.
“The number one challenge was the remote operating context. We don’t have operators on site, we needed a solution that could operate autonomously. We were limited in terms of technologies because we don't have someone to service the asset,” she said.
“The Laramba community is also located on a pastoral lease, which was another challenge. It wasn’t just about engaging with the community, it was also about engaging with the pastoral lease stakeholders, who we had to collaborate closely with.
“We also had a waste management hurdle, the same as with any water treatment plant. All treatment plants create a waste stream and that was one of the trickiest parts of this project.
“We don’t have anywhere on site where we can dispose of uranium waste, which is potentially radioactive. That’s why we went with ion exchange, it had the best recovery and allowed us to design a plant to store waste on site before we can remove it.”
Fit-for-purpose technology
Clean TeQ Water CEO Peter Voigt said remote locations like Laramba pose unique challenges for water treatment solutions, including difficult installation logistics.
“Ion exchange technology was selected for the project for numerous reasons. It is extremely reliable for selective uranium removal to very low levels, with comparatively lower maintenance, energy consumption and waste volumes,” he said.
“Our customised design of the Laramba Water Treatment Plant includes numerous measures to reduce ongoing maintenance and operation requirements.
“The plant is fully automated with advanced real-time monitoring capabilities, allowing remote identification and resolution of potential issues with reduced frequency of on-site visits. The intuitive layout makes it easier for local contractors to perform basic checks and maintenance tasks and reduces the need for specialised technical staff to attend site.
“Ion exchange has a reputation of being a robust low maintenance technology, however redundancy is still built into the system to reduce the risk of downtime with treatment occurring across two parallel trains.”
The scope of work included upgrading the existing equipment on site, including expansion of the bore compound, replacing the bore pumps, as well as installation of tanks, new buildings and the water treatment plant.
Voigt said the importance of community engagement cannot be overstated, with Power and Water Corporation doing a fantastic job involving the community all the way through to the launch event.
"The bench-top testing performed in our laboratory provided a six-month equivalent of real-world operation, confirming the performance of the uranium removal system and allowing potential issues to be identified and eliminated,” he said.
“The Laramba Water Treatment Plant project demonstrates that, with the right technology and planning, safe and secure drinking water can be provided within tight timeframes to remote communities around Australia.
Savouring success
Despite the challenging circumstances, Islam said the project was delivered on time and under budget, a testament to the team’s commitment and collaboration.
"We achieved this through close monitoring at every step to make sure everyone was informed on progress, which allowed us to manage risks up front and mitigate those potential risks before they impacted the project,” he said.
“We had a very committed internal team. All our teams worked together to make this a success, and I do believe that the internal commitment we had to this project played a big part in having it delivered on time.”
Purser said the excellent relationship formed with Clean TeQ Water was also an important factor in the project’s success.
"We had a great relationship with our supplier Clean TeQ. We provided local contractor details to Clean TeQ, so that they had people to work with who were familiar with the area. Having local contractors on the job was integral to this project's success,” she said.
“While remote contexts are not the place for innovation in terms of technology, the way we facilitated the project was certainly innovative. Having agreement from all stakeholders on the scope and outcomes of the project really helped.
“Once the project was completed, we held an open day at the new treatment plant. We all met at the site and celebrated the opening of the water treatment plant, which was well received by the community.”
Islam said seeing the community receive their new treatment plant was very rewarding.
“The community was so happy. The whole community came with their empty water bottles to fill up from the plant. It was a happy moment to see how overjoyed they were, it was really rewarding for us because we are here to service them.”
Interested in nominating an outstanding project for the Australian Water Association’s awards? Take a look at nomination categories here.