Smart tech spots pump problems in real time
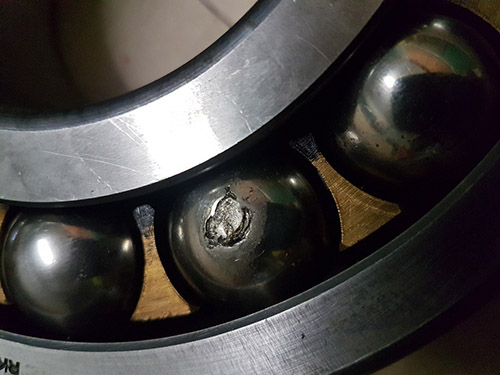
The world is becoming smarter each and every day. With technology advancing at increasing speeds, everything from our watches to our homes is becoming a smart device. The water sector is no stranger to this development.
The water sector is continually evolving, using all the tools available to ensure water and wastewater is treated efficiently and effectively.
The use of smart technology in a routine inspection by Water Engineering Technologies has ensured that a major water pump station continues to operate safely and reliably, moving drinking water to more than 11,000 customers in Adelaide.
Before the emergence and adoption of smart technology, visual and audible inspections of a utility's assets was required. Maintenance included replacing components at fixed intervals, rather than when necessarily needed. Smart technology, however, now allows for accurate insights into the health of the assets, ensuring ongoing reliability and cost efficiency.
A recent inspection of a pump at Sellicks Hill performed by Water Engineering Technologies Condition Monitoring Officer Timothy Tomo involved using a portable analyser to capture data from sensors that were attached to the pump.
The data was then imported into the machinery health analyser, which shows the health of the pump, diagnoses any faults and discloses what requires fixing. On this occasion, Tomo noticed that the overall vibration levels within the pump had risen sharply since the last survey, revealing a rapidly deteriorating pump bearing.
In response, the Water Engineer Technologies maintenance team were able to immediately disassemble the pump, identify the damaged bearing and replace it before the situation escalated. Had it not been identified and dealt with so rapidly, the defect could have caused the pump to fail, further causing significant secondary damage.
According to Lead Condition Monitoring Engineer Stephen Moore, had the fault not been dealt with, SA Water would have had to refurbish or even replace the pump, which, for previous pumps, had cost in excess of $200,000.
“We have replaced traditional visual and audible inspections of assets with portable analysers, and by keeping watch on asset condition parameters, asset health can be readily identified and where possible, rectified,” Moore said.
"We can now make well-informed decisions about the most appropriate time to repair, rehabilitate or replace an asset before failure can occur."
Using the smart technology available, Senior Manager Maintenance Nima Gorjian Jolfaei said the team can take the guesswork out of asset management.
"We no longer simply refurbish or replace components at fixed time intervals based on the rationale that this will reduce the incidence of faults," Nima said.
"In most cases, this sort of scheduled maintenance was based on manufacturers' recommendations, best guesses, or a mixture of both, with very little evidence of root causes of actual or potential failures identified.”
Rather, the smart technology provides real-time information.
“Smart condition monitoring technology provides our team with a much better understanding about why assets wear out, how they behave and how they respond to various operating conditions and environments,” Jolfaei said.
“Our advanced maintenance services are significantly increasing asset reliability and performance and reducing our costs.”
Welcome to the future.