Icon Water trials robotic cleaning for reservoirs
This case study was sourced by the Australian Water Association’s Water Quality Monitoring and Analysis Specialist Network.
Icon Water’s reservoirs are currently drained and cleaned manually by our network maintenance delivery crews every 5 years and it is a very time-consuming and costly procedure. Previously the only method available for tank and reservoir cleaning has been to drain and clean the reservoir, which requires asset downtime.
Icon Water decided to trial a new method and completed the first robotic reservoir cleaning trial at the Fadden reservoir on Monday, 17 September 2018 and Mugga Quarry Tank on Tuesday, 18 September 2018 with the help of Watertight Robotics, Australia’s largest provider of online robotic tank and reservoir cleaning solutions with over 35 years of tank cleaning experience.
Watertight Robotics specialises in safe, economical robotic solutions for the cleaning and inspection of potable storage assets online. Icon Water was the first utility in Australia to utilise the new state-of-the-art robotics truck.
The robot used for the cleaning trial is a potable grade, oil-free unit that can achieve 100% cleaning of potable tanks, including difficult to reach areas. The robot slightly increases turbidity as it moves through the tank. Turbidity was monitored during the cleaning session to verify this claim.
Key benefits of potable robotic cleaning:
- No human entry (hence no confined space entry)
- Lower overall cost
- No thrusters or hydraulic parts
- Assets cleaned online
- Comprehensive inspection capability
- Low impact on water quality
- No discoloured water customer complaints (normally resulted from zoning and de-zoning to put reservoir offline)
- Built and maintained for potable water use
To access the reservoir, the robot was lifted using a crane onto a platform where it was configured and then released slowly into the water tank via the reservoir hatch.
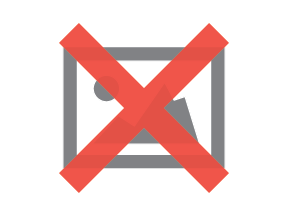
The robot has five mounted cameras that transmit video footage via a telemetry cable to the mobile control room in the truck. An operator uses the live screen display and a control pad to manoeuvre the robot inside the reservoir. The video quality was good and the sediment on the bottom of the reservoir was clearly visible.
A ROV was deployed to perform condition assessment of the reservoir components, including the wall and roof structural members after the cleaning robot completed its operation.
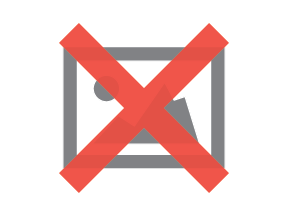
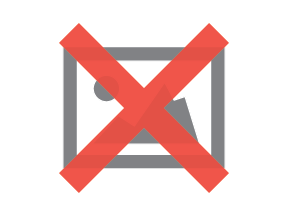
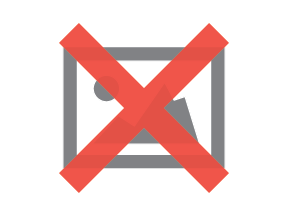
The Water Quality team were on site to monitor the water quality while Fadden reservoir was cleaned. Although the reservoir can be online during the cleaning process, this reservoir was offline during the trial as this was the first time it was used in one of our reservoirs.
Overall the trial went well and the teams were largely satisfied with the end results. Antony and his team from Watertight Robotics were very professional and helpful in answering all the questions the Icon Water team had about the process.
The water quality samples taken during the cleaning process did not suggest a significant impact on water quality caused by the robotic cleaning. Icon Water plans to undertake further trials to confirm the impact on water quality without taking the reservoir offline.
The trial has clearly proven the benefits of robotic cleaning to the team, who will continue to monitor this space for future updates and improvements as the technology continues to evolve.
The trial was a success due to a great teamwork by the team members from operations, water quality, process, risk, safety, engineering services, asset strategy and analytics, maintenance engineering and delivery planning, and network maintenance delivery.
For further questions about the trial cleaning event, please contact Rae Kyaw, Long Term Maintenance Planner – Bulk Water.
For more information on the Australian Water Association’s Water Quality Monitoring and Analysis Specialist Network, click here.